1.4. Получение, строение и свойства химических волокон
Искусственные волокна. С древних времен и до конца XIX в. единственным сырьем для производства текстиль ных материалов служили
натуральные волокна растительного или животного происхождения.
Огромные успехи химии на рубеже XIX и XX вв. создали необходимые
условия для получения и промыш ленного производства химических
волокон. Прототипом получения химических волокон послужил про-цесс образования шелкопрядом нити при завивке кокона.
Впервые мысль о возможности получения искусственного волокна
была высказана еще в XVII в. англичанином Р. Гуком, но в промышленности оно было получено только в конце XIX в. Первые искусственные
волокна из нитрата целлюлозы (нитратный шелк) были получены
1883 г. Несколько позднее появились другие виды целлюлозных волокон: медноаммиачные, вискозные и ацетатные. В середине 30-х гг. XX в.
значительным сдвигом в производстве хи мических волокон явилось
получение первых синтетических воло кон (полиамидных), которое оз-наменовало начало нового этапа – создание волокон с заданными свой-ствами. С тех пор мировое про изводство химических волокон непрерывно и быстро растет. В 1913 г. в мире вырабатывалось 11,8 тыс. т
химических волокон, или менее 0,2 % всего объема текстильного сы-рья. К началу треть его тысячелетия их производство составило примерно 31,3 млн. т., а их доля в общем объеме – 54,2 %. [4].
В мировом балансе текстильных волокон химические занимают
первое место. По данным на 2003 г. их производство составляет 55,2 %
от общего количества выпускаемых в мире волокон. В будущем выпуск
химических волокон будет повышаться, вследствие ряда причин:
–
их выпуск не зависит от климатических условий как, например,
урожайность хлопка или льна зависит от погодных условий,
всхожести и сортности семян;
–
себестоимость химволокон невысока. Например, себестоимость
вискозного волокна составляет 70 % от себестоимости хлопка,
себестоимость капрона – 6 % от себестоимости шелка;
–
волокна обладают рядом ценных свойств – высокая эластичность, устойчивость к действию химических реагентов, светопо-годы. Изделия и ткани из них не сминаются;
–
при переработке химволокон меньше отходов;
–
свойства волокон можно изменять в желаемом направлении
на стадии синтеза или формования.
Химические волокна выпускаются в виде одиночных филаментных
нитей или штапельного волокна [20].По прогнозам на ближайшее десятилетие расширение ассортимента и увеличение производства текстильных волокон будут происхо-дить по нескольким направлениям:
–
совершенствование свойств волокон для широкой области применения за счет их модификации – повышения комфортности
и механических свойств;
–
создание супер волокон со специальными свойствами более узкого
назначения (сверхпрочные, сверхэластичные, ультратонкие и т.п.);
–
создание интерактивных волокон, активно «откликающихся»
на изменение внешних условий (тепло, освещение, механическое
воздействие и т.д.);
–
разработка новых технологий получения синтетических волокон
из воспроизводимого (природного) сырья, чтобы уменьшить зависимость от снижения запасов нефти и газа;
–
использование биотехнологий для синтеза новых видов волокнообразующих полимеров и улучшения качества натуральных
волокон.
Основные этапы получения химических волокон и нитей
Все химические волокна, кроме минеральных, формуют из расплавов или прядильных растворов высокомолекулярных соединений.Несмотря на некоторые различия в получении отдельных видов химических волокон, общая схема их производства состоит из следующих основных этапов:
1. Получение и предварительная обработка сырья.
2. Приготовление прядильного раствора или расплава.
3. Формование нитей.
4. Отделка.
5. Текстильная переработка [4].
Расплав или прядильный раствор определенной вязкости и концентрации фильтруется, очищается от пузырьков воздуха и продавливается через тончайшие отверстия специальных фильер, изготовленных
из химически стойких металлов.
Форма отверстий фильер может быть различна и определяет форму поперечного сечения волокна. Образующиеся при продавливании
раствора или расплава струйки затвердевают и образуют нити. Затвердевание может происходить в сухой или мокрой среде. В зависимости
от этого различают три способа формования:
•
из расплава;
•
из раствора сухим способом;
•
из раствора мокрым способом.
При формовании из расплава (рис. 1.11) тончайшие струйки, вытекающие из фильера, обдуваются струей воздуха или инертного газа,
охлаждаются и затвердевают. При формовании из раствора по сухому
способу (рис. 1.12) струйки попадают в шахты с горячим воздухом, где
происходит испарение растворителя и затвердевание полимера.
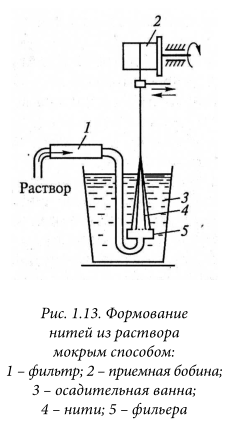
При формовании из раствора по мокрому способу (рис. 1.13) струйки попадают в раствор осадильной ванны, где
происходит выделение полимера в виде
тончайших нитей. Количество отверстий в фильере при производстве комплексных текстильных нитей может
быть от 12 до 100. Сформованные из одной фильеры нити соединяются, вытягиваются и наматываются.
Следующим этапом в получении химических волокон и нитей является их отделка.
Отделка волокон включает ряд операций.
1. Удаление примесей и загрязнений.
Данная операция проводится толь-
ко для волокон, формируемых мокрым способом. При этом готовые
волокна и нити промывают в воде
или специальных раст ворах.
2. Беление. Проводят операцию с целью придания волокнам и нитям
необходимой степени белизны. Ее осуществляют только для волокон, которые будут окрашиваться в светлые тона.
3. Вытягивание и термообработка. Проводят данную операцию
с целью перестройки первичной структуры волокна. При вытягивании макромолекулы выпрямляются, происходит их ориентация
вдоль оси волокна, следовательно, увеличивается прочность волокон, но уменьшается их растяжимость. Термическая обработка
снимает напряженное состояние нити, происходит ее усадка, макромолекулы приобретают изогнутую форму при сохранении
их ориентации вдоль оси волокна.
4. Поверхностная обработка (аппретирование, замасливание и т.п.)
придает нитям способность к последующим текстильным перера-боткам, например, снижает электризуемость.
5. Сушка осуществляется после мокрого формования в специальных
сушилках.
Кроме того, отделка нитей проводится с целью придания им некоторых свойств (мягкости, шелковистости, матовости и т.п.). После отделки нити перематываются в паковки и сортируются. Некоторые
волокна проходят отбеливание или крашение.
Формование
нитей из раствора
мокрым способом:
1 – фильтр; 2 – приемная бобина;
3 – осадительная ванна;
4 – нити; 5 – фильера
Для получения профилированных или полых волокон применяются фильеры с отверстиями сложной конструкции.При формовании получают либо комп лексные нити, состоящие
из нескольких длинных элементарных нитей, либо шта пельные волокна – отрезки нитей опре деленной длины. Текстильная переработка.
Этот процесс предусмотрен для со единения нитей и повышения
их прочности (скручивание и фик сация крутки, увеличения объема
паковок нитей (перематыва ние), оценки качества полученных нитей
(сортировка). При формовании получают либо комп лексные нити,
состоящие из нескольких длинных элементарных нитей, либо штапельные волокна – отрезки нитей опре деленной длины.
Текстильная переработка. Этот процесс предусмотрен для соединения нитей и повышения их прочности (скручивание и фик сация
крутки), увеличения объема паковок нитей (перематыва ние), оценки
качества полученных нитей (сортировка).
Модификация текстильных волокон. Расширение и улучшение ассортимента волокон может, осуществляется не только за счет разработки новых волокнообразующих полимеров, но и путем модификаии (изменения) существующих химических волокон. Модификация
может быть: физической или структурной; химической. При физической модификации проводят направленное изменение строения и надмолекулярной структуры волокон: изменение формы, ориентации,
расположения макромолекул, их длины, введение между макромолекулами дополнительных веществ (без образования химических связей)
и т.п. Наиболее распространены следующие виды физической модификации: ориентация и вытягивание; введение добавок (НМВ) в раствор
или расплав; формование из смеси полимеров; получение бикомпонентных волокон, профилирование волокон. В результате физической
модификации волокна меняют прочность, растяжимость, блеск, матовость, белизну, бактерицидные, огнеупорные свойства, приобретают
сочетание свойств двух волокнообразующих полимеров, устойчивую
извитость и т.д. Ориентацию и вытягивание проводят на стадии формования и отделки волокна для увеличения прочности и устойчивости
к многократным деформациям. При введении добавок в раствор или
расплав добавляют небольшое количество НМ реагентов, которые,
не вступая в химическое взаимодействие с полимером, располагаются
между макромолекулами. Такой вид модификации повышает стой-кость к термической, терм окислительной, фотохимической деструкции, позволяет изменить блеск, придать матовость, увеличить степень
белизны, придать бактерицидные, огнеупорные свойства. Формование
волокон из смеси полимеров предполагает добавление в раствор другого
волокнообразующего полимера, растворимого в тех же растворителях.
Оба полимера участвуют в формировании надмолекулярной структуры, придавая волокну определенные свойства.
Профилирование волокон достигается применением при их формовании фильер, имеющих отверстия различной формы: треугольника,
многолучевой звездочки, трилистника, двойного ромба, щелевидные
разной конфигурации и т.д. Этим способом модификации поверхности волокон придается шероховатость, повышенная цепкость, что повышает объемность и пористость текстильных нитей и материалов
из таких волокон, а также обеспечивает им люстровый блеск, шелковистость и другие ценные свойства.
Получение бикомпонентных волокон заключается в том, что через
фильеру специальной конструкции формуется волокно из растворов
или расплавов двух полимеров, которые соединяются между собой
на поверхности раздела. Бикомпонентные волокна могут быть:
–
сегментной структуры, когда полимеры по сечению волокна располагаются в виде сегментов;
–
матрично-фибриллярной структуры, при которой полимеры мо-гут быть расположены концентрически в виде ядра и оболочки
или в виде более или менее длинных фибрилл одного полимера,
размещенных внутри волокна из другого полимера.
Примером физически модифицированных волокон могут служить
модифицированные вискозные волокна – полинозное и сиблон, которые по своим свойствам приближаются к хлопку благодаря изменен-ной надмолекулярной структуре по отношению к обычному вискозному волокну.
В последнее десятилетие разработаны новые способы структурной
модификации, применение которых позволяет придать химическим
волокнам ценные, но не свойственные для них качества. Благодаря созданию полых синтетических волокон, имеющих один или несколько
каналов или объемные полости, значительно повысили показатели
гигроскопичности и теплозащитных свойств. Образование полых
каналов происходит на стадии формования за счет использования
фильер специального профиля и конструкции. В США и Японии разработаны методы получения многослойных волокон (до 1000 пленочных слоев). Такие волокна способны изменить блеск, цветовые оттенки и насыщенность при смене освещения или угла зрения и даже
обладают голографическим эффектом. Одним из основных направлений совершенствования и улучшения качества химических волокон
было создание сверхтонких волокон, так называемой микрофибры
(от англ. microfi rber). Для этого произвели существенные изменения
на всех этапах производства: уменьшили вязкость растворов и расплавов, разработали и создали более качественные фильеры, изменили условия формования, охлаждения и отделки волокон. Традиционная технология позволяет получать волокна линейной плотностью до 0,01 текс,
а по современной технологии – до 0,00001 текс. Другим способом полу-чения сверхтонких волокон является формование бикомпонентной
нити, состоящей из растворимой матрицы с расположенными в ней
по всей длине тонкими нитями. После удаления матрицы получают
сверхтонкие нити.
Химическая модификация включает методы, частично изменяющие
состав волокнообразующего полимера: синтез волокнообразующих
сополимеров на стадии приготовления прядильного раствора и формования нитей, синтез привитых сополимеров, «сшивание», т.е. увеличение поперечных связей между макромолекулами, химическое пре-вращение полимера при воздействии на него различных реагентов.
Благодаря ей получают волокна с новыми свойствами. [4].Искусственные волокна. Искусственные волокна получают в за-водских условиях из природных веществ органического (целлюлоза,
белок) и неорганического (стекло, металлы) происхождения [14].
Гидратцеллюлозные волокна. Сырьем для производства гидратцеллюлозных искусственных волокон является природная целлюлоза, со-держащая α-целлюлозы 90–98 %. Целлюлозу получают из древесины
ели, сосны, пихты, бука, хлопкового пуха. Выпускаемые гидратцеллю-лозные волокна имеют разные стро ение и свойства.
Вискозные волокна (viscose) (рис. 1.14, а, б) вырабатывают из древесной целлюлозы, получают однованным способом с одновременной вытяжкой, что способствует образованию неодно родной структуры
волокна. Вискозное волокно эластично (ε = 12–14 %), гигроскопично
(W = 35–40 %) и имеет разрывную длину как у хлопка. Оно термостойко, хорошо окрашивается, мягкое, легко драпируется, но пиллингуется, усаживается. Недостатком вискозного волокна является большая
потеря прочности в мокром состоянии (до 60 %). Вискоза выпускается
в виде волокна и комплексной нити (продольно скрепленных волокон).
Действие температуры, светопогоды и микроорганизмов на эти волокна аналогично действию на хлопок и лен. Горят волокна быстро,
желтым пламенем с образование легкого сероватого пепла, с характерным запахом жженой бумаги [26].
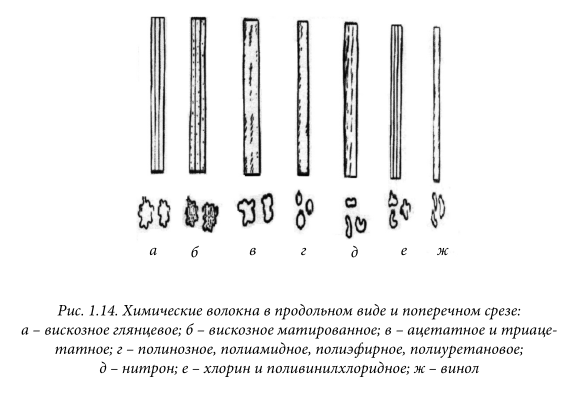
В последние годы химическая промышленность выпускает более
прочные волокна – сиблон (высокомодульное вискозное ВВМ) и полинозное волокно. Сырьем для его получения является вискозное волокно. После осадительной ванны нити пропускают через пластификационную ванну с горячей водой, где они набухают. Затем нити вытягивают,
в результате макромолекулы целлюлозы ориентируются вдоль оси волокна, возникают новые межмолекулярные связи, волокно упрочняется.
Сиблон имеет в 2–3 раза бόльшую устойчивость к действию щело-чей, потери прочности в мокром состоянии не более 25 %. Разрывная
длина сиблона 35 ркм, а разрывное удлинение 8–14 %. Сиблон имеет
круглое поперечное сечение. Это волокно более упругое, менее сминаемое и менее усадочное по сравнению с обычным вискозным волок-ном. Сиблон применяется как заменитель средневолокнистого хлопка,
в смеси с хлопковыми и синтетическими волокнами и в чистом виде.Достоинством всех вискозных волокон является отсутствие спут-ников целлюлозы, что облегчает отделку в отделочном производстве.
Из вискозных штапельных тканей изготавливают костюмы, платья,
бельевой трикотаж. Изделия обладают мягкостью, приятным туше,
шелковистым блеском.Производят гидратцеллюлозные волокна с антимикробными, огне-стойкими и другими важными физико-химическими свойствами.
Медноаммиачное волокно вырабатывается из хлопковой целлюлозы, формуется двухванным спо собом: в первой ванне оно получает
предварительную вытяжку с частичным восстановлением целлюлозы,
во второй ванне вытяж ка завершается. Прядильный раствор получают
путем растворения хлопкового подпушка в медно-аммиачном реактиве. Способ получения волокна мокрый. Осадительная ванна содержит
воду или слабую щелочь.
По физико-механическим свойствам медноаммиачное волокно
аналогично обычному вискозному волокну, но уступает по прочности
и удлинению. Эти волокна тоньше, мягче, меньше блестят, чем вискозные. Химические свойства медноамиачных волокон аналогичные свой-ствам вискозного волокна. При горении медноаммиачные в отличии
от вискозных окрашивают пламя в зеленовато-голубой цвет [15].
Поперечный срез медно-аммиачного волокна имеет округлую форму.
Медноаммиачные волокна вы пускаются в ограниченном объеме
и применяются главным обра зом в трикотажном производстве.Производство вискозных и медноаммиачных волокон связано
с экологическими проблемами, так как требует большого расхода воды,
выделяет токсичные отходы, для очистки которых необхо димы большие затраты.
Ацетатные волокна имеют на поверхности продольные штрихи, бо-лее крупные, чем на вискозных нитях (рис. 1.14, в).Волокна гладкие, чем объясняется скользкость тканей и смещение нитей
в них. Ацетатные волокна тоньше, чем вискозные, поэтому блеск их более
приятный, напоминает блеск натурального шелка. Могут быть получены
профилированные ацетатные нити, дающие искристый блеск, увеличива-ющие объемность и сцепляемость, уменьшающие теплопроводность.
Ацетатные волокна менее гигроскопичны, чем гидратцеллюлозные:
W = 3,5 % у триацетатного волокна и 6 % – у ацетатного волокна. В связи
с этим влияние влаги на их свойства неболь шое. Ацетатные волокна
более прочные и более эластичные ε = 27 %. Горит ацетатное волокно
желтым пламенем, выделяя кислый запах и образуя на конце волокна
наплыв темного цвета, который после охлаждения легко раздавливается
пальцами. Если пламя погасить, то волокно медленно тлеет с выделением
струйки дыма. Триацетатные волокна имеют не высокую прочность
при растяжении, однако обладают высокой упругостью, вследствие чего хорошо сохраняют форму в изделии, а также не усаживаются
при влажной и теп ловой обработке. Из недостатков следует отметить
невысокую термостойкость. Ацетатные и триацетатные волокна термопластичны. При температуре 140–150 °С (ацетатные) и 180–190 °С
(триацетатные) волокна начинают размягчаться, а соответственно
при температурах 230 и 290 °С они плавятся с разложением. Ацетатные
и триацетатные волокна имеют невысокую прочность к истиранию
и трудную окрашиваемость. Изделия из триацетатных и ацетатных нитей не мнутся, устойчивы к действию микроорганизмов, пропускают
УФ-лучи.
Ацетилцеллюлозные волокна характеризуются высокой устойчивостью к действию микроорганизмов, светостойкостью и хорошими диэлектрическими свойствами [1]. Горят волокна медленно, желтым пламенем, образуя на конце оплавленный бурый шарик, при этом ощущается
характерный запах уксуса. Из ацетатных волокон изготавливают трикотажные полотна, технические ткани. Триацетатное волокно используется как в чистом виде, так и в смеси с другими волокнами для изготовления блузочных, платьевых, рубашечных, подкладочных, галстучных
и костюмных тканей, нетканых материалов, а также для технических
изделий. Изделия из триацетатного волокна приятны на вид, обладают
хорошим грифом, подобным грифу натурального шелка, мало загрязняются, мягкие, хорошо драпируются, быстро сохнут после стирки.
Белковые химические волокна. Исходны ми полимерами для произ-водства искусственных белковых воло кон служат казеин (белок молока) и зеин (белок растительного происхождения). Казеиновое волокно
получают из отходов молочной промышленности путем добавления
в молоко кислоты, в результате чего белок свертывается и в виде
творога выпадает в осадок. Затем казеин высушивают, растворяют
в едком натре до получения вязкого прядильного раствора, который
через фильтры продавливают в осадительную ванну, содержащую
формальдегид. Полученные нити замасливают, вытягивают и наматы-вают на специальные патроны.По показателям растяжимости и гигроскопичности казеиновые
и зеиновые волокна близки к натуральной шерсти. На ощупь они мяг-кие, имеет матовый блеск, теплые, хорошие теплоизоляторы. Однако
их прочность невелика и значительно снижается в мокром состоянии.
Термостойкость волокон небольшая, они боятся горячей воды, особен-но содержащей щелочь.
Волокно неперспективное, так как сырьем является пищевой продукт.
Из белков арахиса, сои и кукурузы получают зеиновые волокна [20].
Карбаматные волокна. Карбоцелл – искусственное целлюлозное
волокно, регенерируемое из раствора карбамата целлюлозы, который
получается в результате взаимодействия целлюлозы и мочевины.
Полилактидные волокна. Созданы новые полилактидные волокна
на основе биохимически превращаемых полисахаридов (крахмала), полу-чаемые на основе крахмалосодержащих растительных отходов. В настоящее
время несколько фирм США, Японии и Германии создают современные
технологии получения молочной кислоты полилактида и полимерных
материалов на их основе уже строятся или проектируются крупные про-мышленные производства. Исходным сырьем для биохимического
процесса в основном служит крахмал (маисовый, кукурузный, картофельный) или некоторые другие растительные продуты, содержащие
гексозаны. Эти исходные материалы подвергаются гидролизу с образованием глюкозы и других гексоз. Имеется возможность использования
гидролизата, получаемого кислотным гидролизом древесины (целлюлозы).
Полученные гексозы (глюкоза) подвергаются ферментации с образованием молочной кислоты, которая очищается переводом в дилактид. Последний полимеризуется до полилактида, являющегося плавким полимером с температурой плавления 175–190 °С. Получение
волокон и нитей осуществляется формованием из расплава с последующими операциями вытягивания и релаксации. Получение волокон
и нитей осуществляется формованием из расплава с последующими
операциями вытягивания и релаксации.
Синтетические волокна. Синтетические гетероцепные волокна.
К гетероцепным относятся полиамидные, полиэфирные, полиуретано-вые волокна.
Полиамидные волокна и нити. Полиамиды – синтетические гетеро-цепные волокнообразующие полимеры. Их получают на химических
заводах из продуктов переработки нефти и угля.
В нашей стране выпускают полиамидные волокна и нити различных видов: капроновые (поликапролактам, или нейлон-6), анид (полигек-саметиленадипамид, или нейлон-6,6) и энант (полиэнан-тамид, или нейлон-7). Эти волокна и нити получают из расплава полимера с последующим
вытягиванием и термофиксацией. Исходное сырье для получения капронового волокна – бензол и фенол (продукты переработки каменного
угля) – на химических заводах перерабатываются в капролактам.Полимер, полученный из капролактама, измельчают, промывают
горячей водой, высушивают и сухую крошку подают в бункер машины
для формования нитей. Здесь она плавится при 250 °С и подается
к фильтрам. Струйки охлаждают в шахте с холодным воздухом, а полу-ченные нити замасливают, вытягивают, скручивают, наматывают
на перфорированные патроны и подвергают антистатической отделке.
Процессы производства анида и энанта мало отличаются от процессов производства капронового волокна [14].
Свойства полиамидных волокон и их применение
Полиамидные волокна – самые прочные к истирающей нагрузке,
разрывная длина их составляют 65–80 pкм, доля обратимой деформации 96%, высокоэластичные (ε = 25–35 %), волокна устойчивы к микроорганизмам, сравнительно устойчивы к щелочам, неустойчивы
к кислотам, потеря прочности в мокром состоянии 20–25 %.
Недостатки: низкая гигроскопичность (W = 4 %), высокая электризуемость, пиллингуемость, низкая свето- и термостойкость, уже
при нагрева нии до температуры 160 °С прочность уменьшается
на 40–50 %. При температуре 170 °С капрон размягчается, а при 210 °С
плавится. Недостатком можно считать и чрезмерную гладкость поверхности полиамидных волокон, их малую сцепляемость, в результате чего они плохо смешиваются с другими волокнами, при эксплуатации изделий «вылезают» на поверхность ткани. В настоящее время
разработаны химически модифицирован ные полиамидные волокна
каприлон и мегалон, которые по гигроскопичности (5–7 %) не уступают хлопку, а по прочности, устойчивости к истиранию превосходят
его. Восприимчивость волокон к красителям повы шенная. Изделия
из капрона вытягиваются.
При внесении в пламя капрон плавится, загорается с трудом, горит
голубоватым пламенем. Если расплавленная масса начинает капать,
горение прекращается, на конце образуется твердый шарик бурого
цвета [15]. Полиамидные волокна применяются для изготовления
чулочно-носочных изделий, костюмных и платьевых тканей, брезентов.
Полиэфирные волокна вырабатываются из продуктов переработки
нефти. Полиэфирное волокно получают из диметилового эфира терефалевой кислоты и этиленгликоля. В России полиэфирное волокно
известно под названием лавсан. В Англии – терилен, в США – дакрон,
во Франции – тергаль, в Германии – тревера, диолен, ланол. Полиэфирное волокно получают из диметилового эфира терефталевой кислоты
и этиленгликоля.
Волокно обладает высокой эластичностью (ε = 35 %), разрывной
длиной 50 ркм, упругое, несминаемое, не теряет прочность в мокром
состоянии. К недостаткам следует отнести малую гигроскопичность
(W = 0,4 %), в 10 раз ниже, чем капрона, поэтому в текстильном производстве штапельный лавсан применяется для смешивания с вискозными и натуральными волокнами (преимущественно с шерстью).
С гидрофобностью связана так же высокая формоустойчивость материалов из лавсана во влажном состоянии. Лавсановые волокна обладают шерстоподобным внешним видом, на ощупь они мягкие, теплые,
объемные. Волокно устойчиво к действию химреагентов имеет высокую электризуемость, пиллингуемость, трудную окрашиваемость.
По устойчивости к истиранию полиэфирные нити уступают только
полиамидным, но они несравненно более устойчивы к действию свето-погоды [20]. Полиэфирные нити имеют высокую термостойкость (температура размягчения 235 °С), превосходя по этому показателю все
природные волокна и большинство химических. Они способны выдер-живать длительную эксплуатацию при повышенных температурах.
Полиэфирное волокно в виде штапельного волокна в смеси с шерстью, льном, хлопком, вискозным штапельным волокном используется
для изготовления платьевых, костюмных тканей, а в виде элементарных нитей применяется в технических целях для изготовления транспортерных лент, приводных ремней, канатов, парусов, тентов, электро-изоляционных материалов.
В чистом виде лавсан используется для изготовления швейных ни-ток, кружев, ворса ковров и искусственного меха. Горит лавсан желтым
коптящим пламенем, образуя на конце черный не растирающийся шарик [15].
В настоящее время разработана структурно модифицированная
полиэфирная нить шелон-2 – сложно профильная, тонковолок нистая,
шелкоподобная. Эта нить может использоваться при изго товлении
шелковых тканей для придания им малоусадочности, малосминаемо-сти и хороших гигиенических свойств.
Полиуретановые нити. На основе по лиуретанов разработаны син-етические нити, получившие назва ние спандекс, лайкра, дорластан.
В процессе получения полиуретановых нитей их формование проводят как из расплавов, так и растворов сухим и мокрым способами.
В нашей стране на основе полиуретанов выпускают полиуретано-вые нити, формование которых проводят мокрым способом. Отличи-тельная особенность полиуретановых нитей – их высокая эластичность (разрывное удлинение может достигать 800 %). При удлинении
на 300 % доля эластического восстановления составляет 92–98 %.
Полиуретановые нити обладают хорошими механическими свойства-ми, которые используются для придания текстильным матери алам вы-соких показателей эластичности, упругости, формоустойчивости, не-сминаемости. При этом они в 20 раз больше, чем резиновая нить
обладают устойчивостью к истиранию, устойчивы к светопогоде
и химическим реагентам, прочность их сравнительно невелика.
При нагревании до температуры 150 °С начинается термическая
деструкция, что приводит к повышению жесткости и пожелтению нитей.
Полиуретановые нити применяют в медицине и для производства
трикотажных спортивных и эластичных тканей. Они выступают
в качестве каркасных стержней, вокруг которых навиваются нити
из других волокон.
Синтетические карбоцепные волокна. К карбоцепным волокнам
относятся полиакрилонитрильные (ПАН), поливинилспиртовые
(ПВС), поливинилхлоридные (ПВХ) и полиолефиновые (ПО).
Полиакрилонитрильные волокна. Отечественные полиакрилони-трильные волокна называются нитроном; в США – орлоном, акрила-ном; в Японии – кашмилоном и эксланом. Исходным сырьем для про-изводства нитрона служат полиакрилонитрил и его сополимеры.
Волокно нитрона высокоэластичное (ε = 35 %), прочное (Lp = 39 pkм),
устойчивое к действию света. Эти волокна характе ризуются высокой
термостойкостью: в процессе длительного на гревания при температуре 120–130 °С они практически не изме няют своих свойств. Температура размягчения нитрона 200–250 °С. Он стоек к действию минеральных кислот, щелочей органических растворителей при химической
чистке одежды, к действию бактерий, плесени, моли [14]. Нитроновые
волокна имеют шерстоподобный вид, низкую теп лопроводность, показатели которой близки к теплопроводности шерсти. Они обладают
инертностью к загрязнителям, поэтому из делия из них легко очищаются.
Вместе с тем ПАН имеет низкую прочность к истиранию (уступает
даже хлопку), низкую гигроскопичность (W = 1–2 %), высокую электризуемость и больщую склонность к пиллингу.
Полиакрилонитрильные волокна используются для производства
верхнего трикотажа, летнего и зимнего, тканей для занавесей и тентов.
Нитроновые волокна используются главным образом как заменители
шерсти при производстве ков ров, искусственного меха, а также как теплоизоляционный мате риал и добавка к шерстяным волокнам при изготовлении
текстиль ных материалов. При внесении в пламя нитрон плавится и горит ярким, желтым, коптящим пламенем со вспышками, на конце остается темный наплыв неправильной формы, легко раздавливаемый пальцами [4].
Поливинилспиртовые волокна. Эти волокна синтезируют из винилацетата, полимеризуя его до поливинилацетата. К поливинилспиртовым водонерастворимым волокнам относятся винол, летилан. Винол
вырабатывают из поливинилового спирта. Это наиболее дешевое волокно из всех синтетических волокон. Поливиниловый спирт (ПВС)
растворим в воде. Формование волокна осуществляют из водного раствора, в осадительной ванне используют растворы солей (сульфат аммония или натрия). Полученное волокно легко растворяется в воде.
Поэтому его используют в медицине как нити для швов, не требующих
удаления, а также в военном деле для изготовления парашютов, прикрепляемых к морским минам. Для придания волокнам нерастворимости в воде их дополнительно обрабатывают формальдегидом (СН2О).Поливинилспиртовые волокна в России называют винол, в Японии –
куранол, винилон, в США – винал.
Волокно прочное (Lp = 35 рkм), эластичное (ε = 7–25 %), по гигроскопичности (W = 4–5 %) приближается к хлопку, устойчиво к истиранию, характеризуется высокой теплостойкостью., термопластично –
температура размягчения волокна равна 200–230 °С, светостойко [1].
Волокно устойчиво к действию микроорганизмов и бензина, поэтому
используется для изготовления бензошлангов. Хемостойкость у винола меньше чем у других синтетических волокон. При внесении в пламя
волокно дает тепловую усадку, плавится и затем медленно горит желтоватым пламенем.
Винол применяется в чистом виде и в смеси с хлопком, шерстью
и другими волокнами для изготовления бельевых, плательных и костюмных тканей, швейных ниток и разнообразных изделий.
Летилан – водорастворимое волокно желтого цвета, применяется
в медицине при создании предметов личной гигиены, так как обладает
антимикробными свойствами и [14].
Водорастворимая разновидность поливинилспиртовых волокон
используется в текстильной промышленности в качестве вспомогательного (удаляемого) волокна при производстве ажурных изделий,
тонких тканей, материалов пористых волокнистых структур, а также
при изготовлении гипюра (взамен натурального шелка).
Полиолефиновые волокна. Наиболее привлекательны для текстильной промышленности полиэтиленовые и полипропиленовые волокна
из-за широкой сырьевой базы (пропилен и этилен получают при крекинге или пиролизе нефти).
В России их называют полипропилен и полиэтилен, в США – политен, в Англии – курлен, в Италии – мераклон. Полиэтиленовые и полипропиленовые волокна имеют очень прочную, упорядоченную структуру молекул, высокие прочностные и электроизоляционные свойства.
Они гидрофобные, не горят, по весу являются самыми легкими
и для них характерно явление пиллинга.
Полиолефиновые волокна и нити характеризуются высокой устойчивостью к действию кислот, щелочей, не ус тупают по показателям
хемостойкости хлорину. Их устойчивость к истиранию ниже, чем полиамидных нитей, особенно полипропи леновых.
Теплостойкость полиолефиновых нитей небольшая. При температуре 80 °С полиэтиленовая нить теряет около 80 % первоначальной
прочности. Гигроскопичность нитей почти равна нулю, поэтому окрашивание их возможно только введением пигмента в полимер перед
формованием. С низкой гигроскопичностью связана и значительная
электризуемость этих нитей. Плотность полиэтиленовых и полипро-пиленовых нитей очень низкая, поэтому изделия из них не тонут в воде.
Полипропиленовые нити используют в производстве ковров и нетканых материалов. Изделия из полипропилена экологичны, химически стойки к агрессивным и биологическим средам. Плотность поли-пропиленового волокна очень низкая, поэтому изделия из них не тонут
в воде. Они широко применяются в медицине, строительстве, в производстве канатов, фильтров, технических тканей, веревок, гибких
объемных контейнеров, геотекстиля, изоляционного материала, рыбо-ловных снастей, отделочных автомобильных или укрывных материалов для сельского хозяйства.
Среди полиолефиновых волокон наибольшую долю (85 %) составляют
полипропиленовые волокна. Они выпускаются в виде штапельных волокон, текстурированных нитей, расщепленных пленок и лент. Полипропиленовые волокна используют главным образом для технических
целей, а также в производстве нетканых материалов и в смеси с гидрофильными волокнами (хлопковыми, шерстяными, вискозными и др.)
в производстве материалов для верхней и спортивной одежды, обуви,
декоративных материалов.
В настоящее время разработана технология производства волокон
из сверхвысокомолекулярного полиэтилена (НРРЕ). Эти волокна мож-но применять в области баллистической защиты, для производства
фехтовальных костюмов, канатов, сетей и т.д. Они не теряют свою
прочность в воде и не подвергаются воздействию УФ-облучения
и морской воды [20].
Поливинилхлоридные волокна. Исходным сырьем для получения
хлорина и поливинилхлоридного волокна служит этилен и ацетилен.
Поливинилхлоридное волокно обладает высокой химической стойко-стью, устойчиво к действию минеральных кислот, стойко к действию
щелочей, спирта и бензина. Набухает в эфирах, не гниет, устойчиво
к микроорганизмам, морозоустойчиво. Волокно обладает электро-
и звукоизоляционными свойствами, имеет низкую тепло- и водопроводность, теплопроводность в 1,3 раза ниже, чем у шерсти и в 1,8 раза
ниже, чем у хлопка. Волокно не гигроскопично.
Хлорин обладает стойкостью к действию воды, кислот, щелочей,
окислителей, не растворяется даже в смеси концентрированных кислот (в «царской водке»). Волокно не гниет, не повреждается плесенью
и молью. Для хлорина характерно отсутствие блеска и меньшая упругость по сравнению с другими синтетическими волокнами. По теплоизоляционным свойствам волокно не уступает шерсти, гигроскопичность
очень низкая – 0,1%. Хлорин имеет невысокую стойкость к действию
светопогоды. Основной недостаток хлорина – низкая термическая
стойкость. При температуре 70 °С дает полную тепловую усадку,
а при 90 °С полностью разрушается. Хлорин не горит и не поддерживает горения. При внесении в пламя волокно спекается, ощущается запах
дуста. Хлорин электризуется, поэтому так же, как ПВХ-волокно,
используется для лечебного белья. Применяется для изготовления
рельефных шелковых тканей, ворса ковров и искусственного меха,
спецодежды для рыбаков, лесников и рабочих химической промышленности. Модифицированные волокна – винитрон и совиден характеризуются повышенной термостойкостью [14].
Фторсодержащие волокна. К фторсодержащим волокнам относятся
фторлон и тефлон, сырьем для получения, которых являются фторсодержащие сополимеры. Фторлон и тефлон обладают высокой стойкостью
к агрессивным химическим средам, лучшей устойчивостью к свету
из всех известных текстильных волокон. Они негорючие, имеют очень
малую гигроскопичность. Фторлон даже при нагревании до 120 оС
незначительно меняет свою прочность. Это волокно используют для
производства технических тканей, спецодежды, прокладок и т.д.
Тефлон является самым гидрофобным из всех текстильных волокон
и выдерживает действие температур до 300 °С. Разрывная длина тефлонового волокна составляет 17 ркм, а разрывное удлинение – 13 %.
Это волокно гибкое, эластичное. Оно используется для создания тефлоновых имплантатов.
Арамидные волокна. Арамидное волокно представляет собой ароматический полиамид – полипарафенилентерефталамид. Впервые это
волокно было получено в 60-х годах прошлого столетия в лаборатории
химического гиганта DuPont. На рынок оно было выпущено в 1975-м
году под торговой маркой Кевлар. Материалы из арамидных нитей
и волокон (Кевлар, СВМ, Армос, Русар, Тварон) обладают прочностью
при растяжении, упругостью, низким относительным удлинением при
разрыве. Они обладают высокой термостойкостью, стабильностью
размеров, жаропрочностью и огнестойкостью. К их свойствам относится стойкость к коррозии, к действиям химических реагентов, биостойкость, морозостойкость. Они не проводят электрический ток, незначительно меняют свои свойства в мокром состоянии. Среди
ароматических полиамидов (арамидов) российское волокно Армос занимает первое место одновременно по двум основным показателям:
механической прочности и устойчивости к открытому огню. Прочность на растяжение составляет от 4400 до 5500 МПа. Они безусадочные, могут длительно храниться без изменения свойств, незначительно меняют свойства в мокром состоянии, устойчивы к длительному
пребыванию в воде, биостойкие. Арамидные материалы используют
для изготовления композиционных материалов, деталей летательных
аппаратов, средств безопасности и спасения, сверхпрочных канатов
для подъема затонувших судов, текстильных «мягких» и композитных
«жестких» бронежилетов, касок, щитов и многих других изделий.
Сравнительная характеристика получения, строения и свойств, наиболее широко применяемых видов химических волокон представлена
в таблице 1.2.
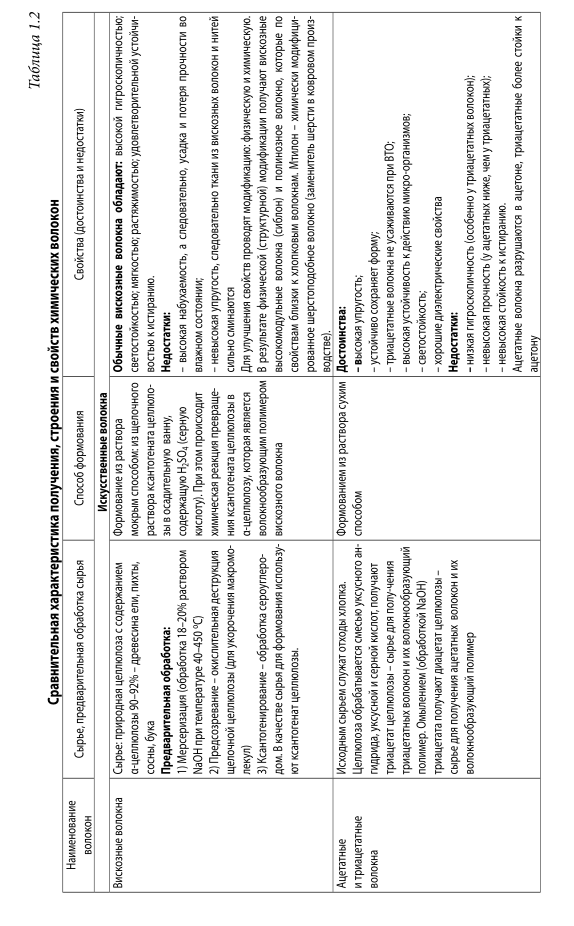
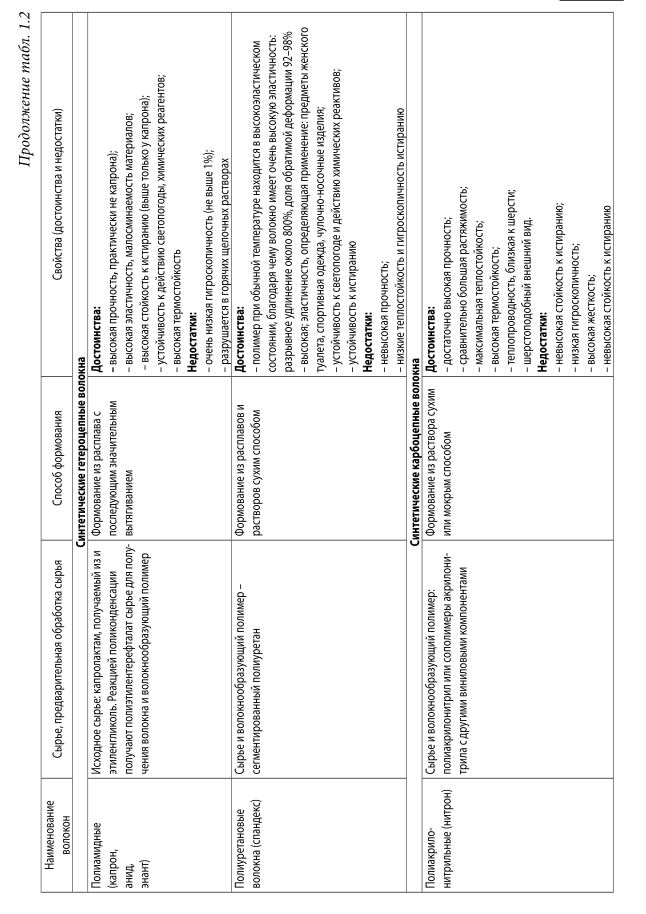
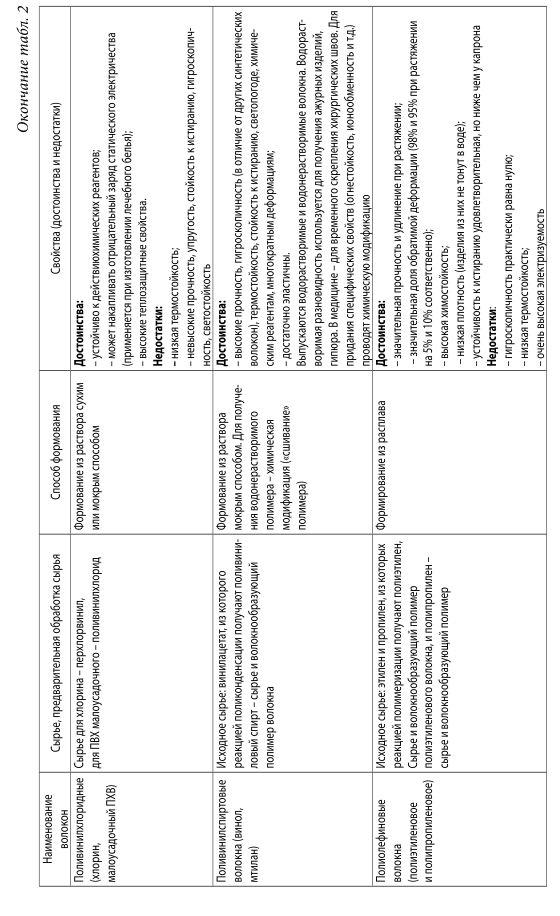 |